Top 7 Elevator Maintenance Mistakes to Avoid
Avoid the most common elevator maintenance mistakes that lead to breakdowns and safety issues. Learn expert tips from a top elevator company in Saudi Arabia.
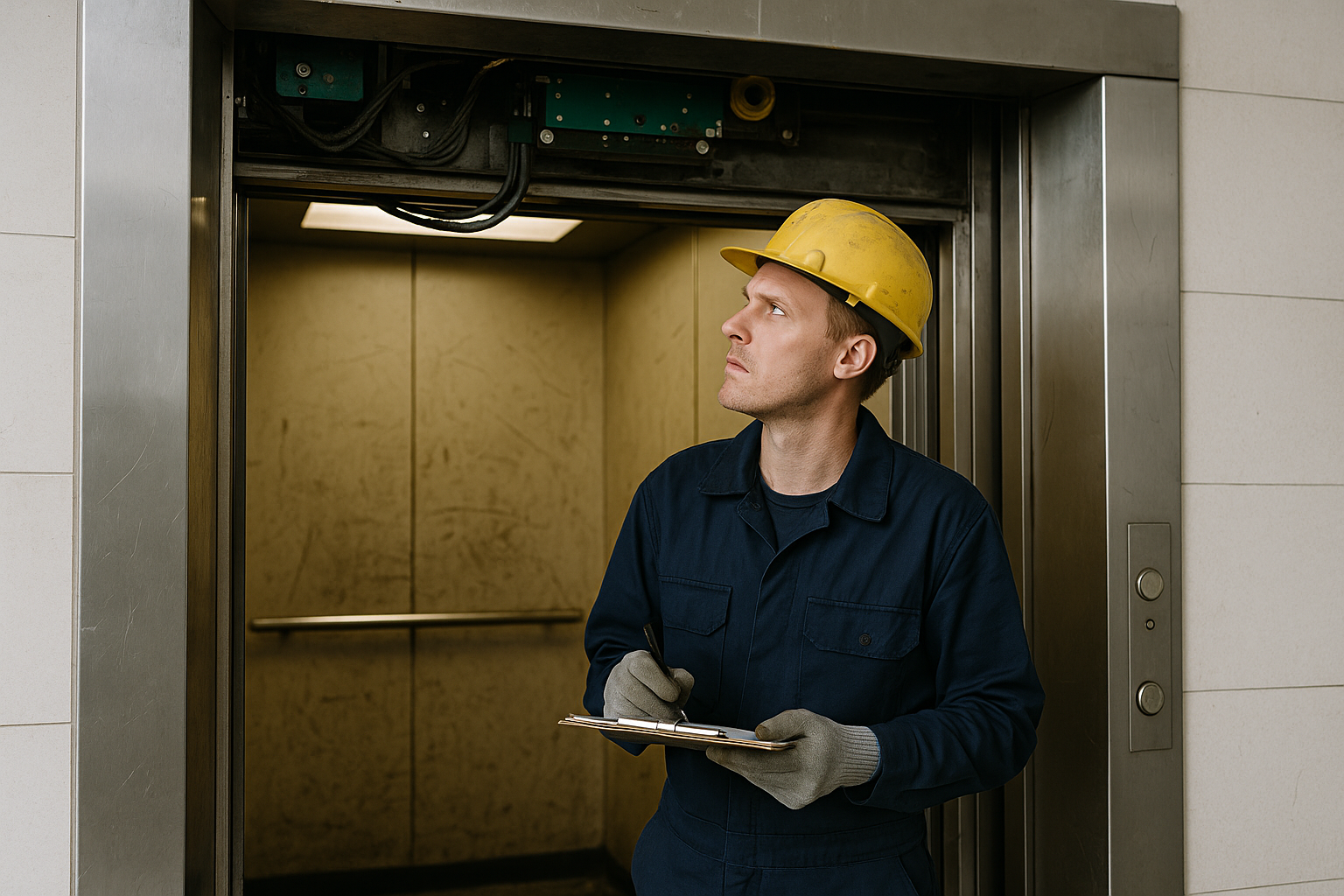
Elevators are engineered for reliability — but only if they’re maintained properly. At SEMAG Elevators, we’ve seen how even small missteps in maintenance can lead to major disruptions, costly repairs, or safety hazards. Whether you manage a warehouse, a residential tower, or a commercial complex, avoiding these common pitfalls is essential to protecting your investment and ensuring the safety of everyone who rides.
1. Skipping Routine Maintenance
Failing to schedule consistent maintenance is the most common and costly mistake. Elevators may seem fine on the surface, but wear and tear build up internally over time. Ignoring routine checks can cause gradual damage to mechanical and electrical components — especially in electric elevators or heavy-use cargo elevators.
2. Using Unqualified Technicians
Elevator systems are complex, and not every technician has the certification or experience to handle them safely. Unqualified service can result in improper adjustments, missed warning signs, or non-compliance with local regulations.
3. Ignoring Warning Signs
Strange noises, jerky stops, longer wait times — these aren’t just quirks. They’re early indicators of problems like motor issues, misaligned guide rails, or faulty sensors. Ignoring them can lead to major breakdowns and even safety risks.
4. Delaying Spare Parts Replacement
When parts start to fail, delaying replacement can compromise the entire system. A worn-out cable, failing brake, or outdated controller can all cause operational issues — or worse, accidents.
5. Poor Maintenance Documentation
Inconsistent or incomplete recordkeeping can create compliance issues and make it hard to track recurring problems. This is especially risky in regulated sectors or for elevator types that require detailed safety inspections.
6. Overlooking Specialized Elevators
Not all elevators are created equal. Elevators without foundation, panoramic lifts, or high-load cargo elevators each require specific maintenance protocols. Applying a one-size-fits-all approach often leads to inefficiencies or missed service needs.
7. Delaying Modernization When Needed
Maintenance has its limits. If your elevator is over 20 years old, no amount of lubrication or inspection will match the safety and performance of a modern system. Continuing to operate outdated equipment increases the risk of failure and non-compliance.
How SEMAG Prevents These Mistakes
As a trusted elevator company in Saudi Arabia, SEMAG provides a comprehensive approach to elevator maintenance that goes beyond routine check-ups. We don’t just respond to problems — we prevent them with proactive, detail-driven service tailored to your building and elevator type.
Our elevator maintenance programs are built around precision, compliance, and longevity. Whether you operate electric elevators in a commercial complex, a home lift in a private residence, or a cargo elevator in a logistics center, SEMAG ensures each system is maintained to the highest standards.
Our full-service maintenance offering includes:
- Certified and experienced technicians
- Scheduled maintenance tailored to elevator usage
- Fast access to genuine spare parts
- Real-time diagnostics and reporting
- Full documentation for compliance
- Custom care plans for all elevator types — including elevators without foundation
With SEMAG, you're not just maintaining an elevator — you're ensuring performance, safety, and long-term value with every service visit.
Get expert guidance and reliable maintenance tailored to your needs.